In a dark green, metal-sided building on the outskirts of Agawam, Massachusetts, sandwiched between a gas station and an old paper manufacturing plant, lives a facility that represents what some say is a key part of the future of organics management: Vanguard Renewables’ $1 million depackaging operation.
The machine was running on idle during a recent tour, with remnants from a previous load of tofu containers, (many still in their cardboard wholesale boxes) strewn across the metal walking floor where materials get dumped. When the depackager is processing a load, the planks of the walking floor move back and forth, funneling packaged goods into a double auger that moves the material up a shaft. The double auger then dumps the material into the massive red stainless steel cylinder housing the heart of the machine: the many-paddled separator.
Although the separator looks like a hammer mill, “it doesn’t actually hammer — it kind of squishes the material out,” said John Hanselman, Vanguard’s founder and chief strategy officer, looking not unlike a captain venturing down into the engine room of the ship as he stood on the staircase leading down to the separator. “Whether it’s a tofu container or a yogurt cup, the idea is to keep the container intact and to get all of the organic material out.”
In addition to its Agawam facility, which processes around 100 tons of organics a day, Vanguard has plans in the works to build six more depackagers in various states. At their new facilities, Vanguard will also install magnetic sorting systems to pull out aluminum cans after the centrifugal process opens up the packaging.
And Vanguard’s not alone; depackagers are cropping up around the country. Nine states now have laws in place banning or discouraging large businesses, institutions — and, in some cases, households — from sending food waste into landfills or incinerators, which has spurred growth in organics recycling. And even in areas without policies in place, companies are increasingly looking to divert their organics to be more sustainable and save on rising disposal costs.
Proponents say depackagers can increase the overall amount of organics being recycled by cutting down on the labor needed to hand-separate spoiled food from packaging. But as the sector expands, so do concerns that compost and fertilizer made from organics that have gone through depackagers could contain microplastics and even PFAS found in food packaging. Critics argue that, with a lack of studies and standards in place in most states, depackagers could be contaminating farms where those materials are applied. Regulators in multiple states are taking a closer look at the issue.
“It’s better to keep our (organic) materials clean and segregated to have higher value end products,” said Brenda Platt, director of composting for the Institute for Local Self Reliance. “You know — garbage in, garbage out.”
Growth in the U.S. depackaging sector
Depackagers were first developed in Europe in the 1990s in response to mad cow disease outbreaks, which prevented wasted food from being used for animal feed, according to a 2019 presentation given to Vermont state officials by Craig Coker, head of Coker Consulting. Early models were based on hammer mills used to grind wood, but the high amounts of force in these initial machines contaminated the food slurry with packaging materials.
The technology has gained popularity in recent years among U.S. waste managers.
“The growth in depackaging ties back to states that have organics diversion legislation,” said Debra Darby, manager of organics sustainability solutions for Tetra Tech, adding that bans on disposing food waste typically start with the commercial sector.
Organics recyclers are also turning to depackagers to lower contamination of feedstock for anaerobic digesters and composters, and to offer grocery stores and food manufacturers in states without food diversion requirements an easy organics recycling option that’s competitive with disposal tip fees. In 2015, Maine-based food waste collection and processing company Agri-Cycle opened the first depackaging facility in the Northeast. The food slurry from Agri-Cycle’s depackager, which is located on a dairy farm just south of Portland, Maine, is mixed with manure in an anaerobic digester.
Holden Cookson, brand manager for Agri-Cycle, said the motivation for buying the depackager was to “lower the barrier to entry” for area grocery stores and other businesses to recycle their food waste. Maine does not currently have a ban on disposing food waste.
Agri-Cycle found that grocery store employees faced a tradeoff between duties like helping customers and taking the time to open packaging and properly compost waste food. “When you think of the footprint of tens of thousands of employees, it’s immense and it really adds up,” said Cookson.
Agri-Cycle has helped regional grocery store chain Hannaford divert all of its food waste from landfills. The grocery store chain was able to reduce its waste hauling costs by around 40% in the process, according to Cookson. Contracts with Hannaford also helped bring down food waste hauling costs for other businesses throughout New England.
On the other side of the country in California, the Salinas Valley Solid Waste Authority installed the same type of depackager that Agri-Cycle and Vanguard use in 2020.
Patrick Mathews, the waste authority’s general manager, said the entity bought the depackager with a state grant as part of an overall effort to help businesses and residents comply with California’s short-lived climate pollutant law, which requires recycling to help cut organic waste disposal 75% by 2025.
Around 70% of the salad greens grown in the U.S. come from the fertile Salinas Valley — meaning the local waste authority deals with a lot of wasted greens.
“The only other option, and we've had some of our packing plants try this in the past, is to have employees open every box, every bag and dump it out,” said Mathews. “Not only is that dangerous, it's impossible… especially if you have a recall.”
Like other depackager operators around the country, the Salinas Valley Solid Waste Authority found another waste stream to run through the machine: source-separated food waste. That material is routinely contaminated with plastic food packaging, containers and other items, creating headaches for operators of compost systems and anaerobic digesters alike. The waste authority puts food waste through the depackager to remove contaminants prior to composting it, Mathews said.
Studies have shown, though, that the mixture of packaging and other contaminants in source-separated organics can be harder on the machines.
The Vanguard vision
Vanguard Renewables got its start building on-farm anaerobic digesters that blend manure with food waste, but they weren’t seeing the levels of incoming food waste that they’d hoped for, according to Hanselman. “What we realized was to really service and truly extract the organic component from the marketplace, you have to provide all this,” he said during the tour of the Agawam facility, gesturing to the thrumming machine.
The depackager, a Scott Turbo Separator, contains screens that further clean the congealed organics, which Vanguard keeps at over 75% liquid by blending them with outdated beer. The liquified food slurry is piped from the depackager to one of four 25,000-gallon storage tanks on the far side of the building. The packaging, meanwhile, goes onto another conveyor belt to be dumped into a receiving dumpster, or, in the case of a single-item load, recycled.
Near the food slurry storage tanks were pallets stacked with boxes of donut croissant dough, macadamia nut cookie dough and lasagna sheets that were destined to be animal feed. “We triage all the inbound loads for the highest and best use” of the food waste, said Hanselman.
As we walked outside the depackaging facility, a silver tanker truck pulled up and began piping in liquid food slurry to go to an anaerobic digester. The food slurry, mixed with manure, gets sent to five Vanguard-owned digesters in Massachusetts and one in Vermont.
Sending food waste to Vanguard’s Massachusetts depackager will be 20% cheaper than sending it to the landfill, said Hanselman, adding that he expects customers to save around that much in most other markets they’re entering. Vanguard’s new facilities will be near major cities or food manufacturing hubs in Denver, New York, Atlanta, Chicago, St. Louis and Kansas City, Missouri.
“Any major metro in the United States should have one or more of these systems,” Hanselman said.
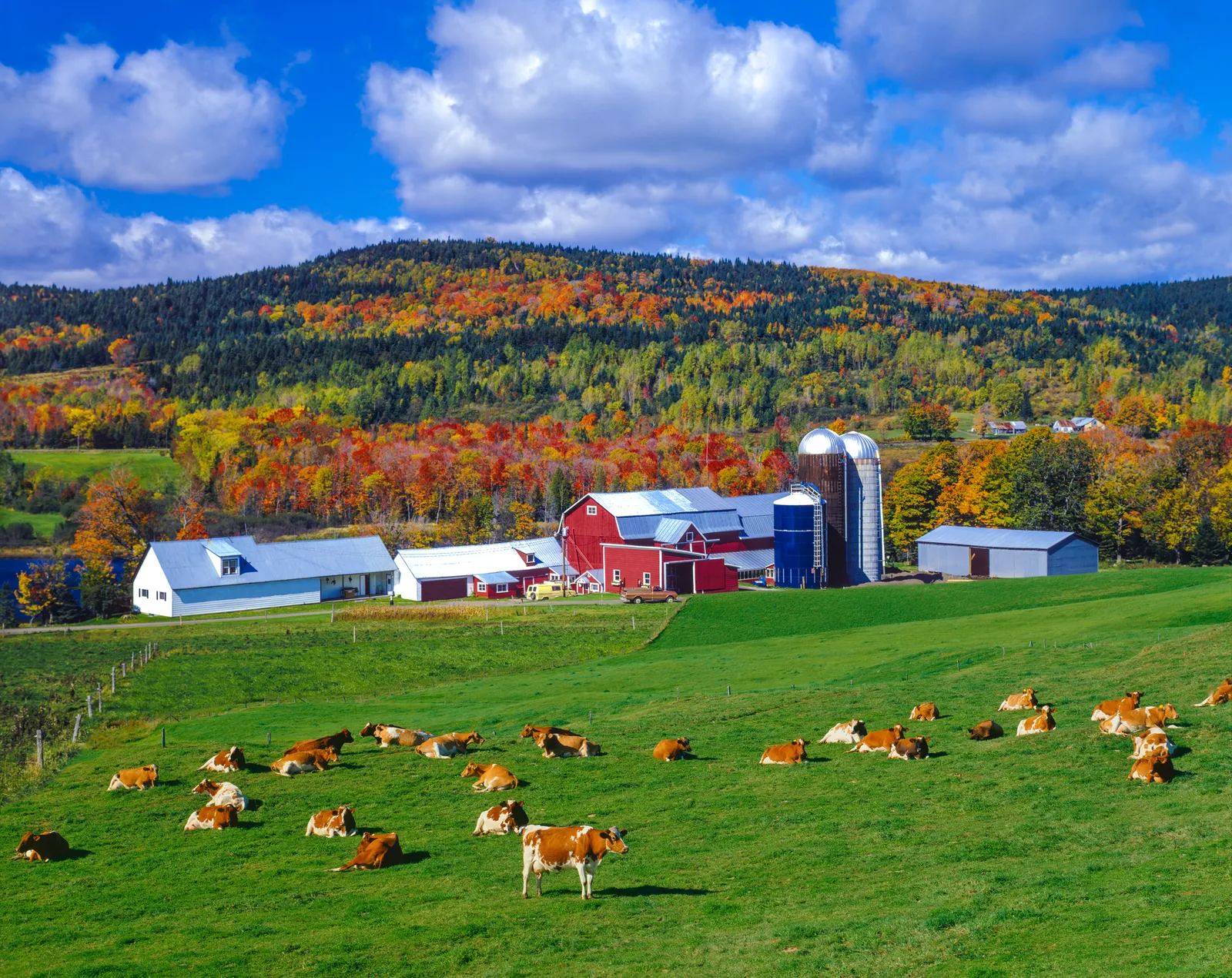
Microplastics and PFAS contamination concerns
Not everyone shares Hanselman’s enthusiasm for depackagers, though. A new depackager in Vermont drew the ire of a coalition of farming, environmental, and composting groups, who raised concerns that it would contaminate fertilizer — and therefore, farms — with microplastics and even PFAS, which stands for per- and polyfluoroalkyl substances.
A third of the state’s food waste is packaged, according to the University of Vermont, and state residents and businesses alike are now banned from tossing food scraps into the trash.
Casella Waste Systems built a depackager last year near Burlington, Vermont, aimed at helping area food manufacturers like Ben and Jerry’s keep spoiled products out of the landfill. The food slurry from the Casella depackager goes to anaerobic digesters, and the leftover digestate is made into fertilizer.
There’s a growing body of evidence showing that microplastics and PFAS are widespread on farm soils, and that vegetables can take up both contaminants. PFAS, in particular, have gained notoriety lately after farms in Maine and elsewhere have shut down upon finding that sewage sludge spreading had contaminated their land and livestock with the compounds. Maine recently enacted a law banning sewage sludge from being spread on farm fields in an effort to stem PFAS contamination.
Concerns about potential negative health effects of certain kinds of PFAS keep growing, including types of cancer, reproductive issues and liver disease. While researchers are still figuring out the health effects from eating PFAS-contaminated foods, environmental health experts caution about cumulative exposure to PFAS from a number of sources. Less is known about the health effects of microplastics, although scientists are concerned that the particles can cause inflammation and damage airways in a similar fashion to wildfire smoke.
Vermont lawmakers looking at the issue initially proposed setting a standard that digestate and soil amendments could have physical contamination levels, including microplastics of no more than 0.5% by dry weight. That standard was nixed in favor of a revised law passed this June that requires the state’s environmental agency to halt issuing any new permits for depackaging facilities until it studies microplastics and PFAS contamination from the facilities and establishes permitting standards.
There’s limited data on microplastics levels in compost and digestate, and even less information on microplastics contamination from depackagers, said Kate Porterfield, a UVM PhD student researching the issue.
Porterfeld and other UVM researchers recently completed a review of existing studies (which is still a pre-print), finding that microplastics levels in compost and digestate ranged anywhere from tens to tens of thousands of particles per kilogram. What the study “drove home for us was that plastics in organics recycling is a systemic problem,” said Porterfield. “And it is definitely not just something that's unique to systems that are using a depackager.”
Additionally, the study authors note that there are other potential sources of microplastics on farms, such as plastic-coated fertilizer pellets and mulch.
In a 2021 study on food waste contamination, the U.S. EPA notes that plastics have “repeatedly been observed” in finished compost. In some cases, compost system and anaerobic digester operators will reject incoming food waste because of plastic contamination streams, meaning the organics are disposed.
The agency added that depackagers and other pre-processing technologies can lower plastic contamination, but that it’s “unclear the extent to which these technologies may inadvertently introduce microplastics or nanoplastics into the end product.”
Porterfield is now studying microplastics levels in depackager food slurry from a uniform food manufacturing waste stream — in this case, ice cream tubs — and source-separated municipal food scraps. The UVM researchers are also analyzing what types of plastic are showing up in depackaging food slurry to see if certain kinds are more or less likely to shatter.
“I think that’s the direction we need to go in — redesigning packaging so it’s compatible with the disposal of food if it becomes wasted,” she added.
What’s next
Four states — California, Maryland, Washington, and Ohio — already have weight-based standards for plastic contaminants in compost; some other states have more general standards for all physical contaminants. Only California has a standard that also pertains to plastics — specifically, plastic film — in land-applied digestate. Porterfeld noted that there’s a “disconnect” between these weight-based standards and scientific studies of microplastic contamination in soil amendments, which generally count the number of plastic particles, meaning the current regulations are not necessarily grounded in science.
Vermont’s not the only state where regulators are taking a closer look at depackagers. A couple of years ago, a Pennsylvania dairy farm with an anaerobic digester installed a Scott Turbo depackager to clean up the food waste it was putting into the digester, as reported by BioCycle. But when the farmer reached out to the state Department of Environmental Protection about using the food slurry from the depackager in other digesters, the agency and farmer were concerned to find visible plastic particles in fields where the digestate was spread.
These concerns prompted the department to amend the farm’s permit for the depackager, requiring that there are “no visible plastic particles” in both the digestate and areas where its land-applied.
Given the widespread use of PFAS in food packaging, experts say it’s no surprise that the compounds are also turning up in compost. The EPA, in a report out last year, said that studies have found PFAS levels in compost to range from 2.3 to 75 micrograms per kilogram, with compost made from food waste having higher levels than that made from yard waste.
Compost and environmental advocates recently testified in both New York and Vermont that states should promote source separation of organics, including separation from packaging, and proper education to create as clean of an organics waste stream as possible from the outset.
ILSR’s Platt said her group isn’t completely opposed to depackagers. But the organization does oppose state environmental agencies setting rules that promote mixing of organics and other waste, an approach she feels was taken in New York.
Last year, New York environmental regulators were developing regulations to implement the state’s ban on large food waste generators disposing of organics, which went into effect at the start of 2022. The state’s Department of Environmental Conservation requires that businesses and institutions separate organics from other materials before they’re collected, but generators are exempt from that requirement if they’re sending the food waste to a facility that can clean it.
“States could require that, if you’re a supermarket and you’ve got rotting potatoes or clementines, you’re not allowed to commingle your unpackaged wasted produce with your packaged stuff,” Platt said.
Vanguard said that ideally, non-packaged organics would stay separate, and that a few of its partners grind unpackaged organics at the store into a slurry to go directly to a digester. But few stores have the capacity to do that, and Vanguard’s goal is to make organics recycling as simple as possible.
“For a store to have to send packaged waste to one location and the loose organics to another would not be cost-effective for them, and more likely than not it would end up in the landfill or harmful incinerator,” said Billy Kepner, Vanguard’s public relations manager, via email.
When asked about microplastics contamination concerns during the tour, Hanselman said that America has an addiction to cheap food wrapped in plastics — and that it would be challenging to eliminate microplastics from the organic waste stream until the amount of plastic packaging is reduced. Vanguard has talked with grocery store clients about using more cardboard packaging when possible.
The company does not currently test their food slurry or digestate for microplastics, and is not currently required to in the states it operates in. Vanguard is not concerned about microplastics impacting its ability to market digestate or use it as a soil amendment on partner farms as the screening processes it uses extracts as much non-organic material as possible, Hanselman said.
“Plastics are just a disaster — there are real problems,” he said. “And as the last guys on the chain handling it, we’re definitely trying to be better at it. But this is a global problem.”