As Greater Boston sees growing numbers of cranes in the skyline and roll-off containers in the streets, operating in the construction and demolition recycling industry that supports this building boom is only getting more complicated.
State regulators say that C&D separation requirements enacted three years ago are an essential piece of their waste reduction strategy, even if they may be affecting processing speeds at recycling facilities.
Operators of those facilities say they’ve invested in the necessary technology to meet these standards, though some have struggled to find markets for certain materials. Others have sold their businesses to bigger companies who have the capital to handle the requirements of this new system. Haulers say they’re often driving farther, waiting longer and paying more to tip their loads than in years past.
With in-state landfill capacity for C&D material projected to be “virtually zero” by 2030, and out-of-state options becoming more limited, the state’s Department of Environmental Protection said in 2021 it aims to “more than double current C&D recycling tonnage.” This would mean cutting C&D disposal volumes by nearly 260,000 tons per year. One of MassDEP’s primary strategies is a minimum performance standard (MPS) for C&D recycling facilities to achieve a 15% process separation rate, on top of existing waste bans for many materials.
Meanwhile, as Greater Boston continues to see numerous construction projects of all sizes, some industry sources say more work is needed to create options for lower-value materials in the stream.
"We're trying to be anti-landfill, but at the end of the day these landfills are going to get a premium because they're the only solution for a lot of this waste,” said John Thomas, a board member of the Construction & Demolition Recycling Association. "The 15% isn't the problem, it's the 85% that's the problem.”
The industry has largely welcomed the MPS as a way to level the playing field for investments in new processing equipment. But combining that approach with the recent inflation in labor and transportation costs has played a role in operating challenges and market consolidation. Many local C&D facility operators have sold their businesses to vertically integrated companies such as WIN Waste Innovations, Waste Connections and Republic Services during this period. Some have shut down entirely.
C&D disposal tip fees are now generally higher than those for MSW in the area and haulers often report multi-hour wait times to tip their loads. Other recent challenges, such as an averted rail strike and the temporary collapse of markets for wood (a top commodity in the stream), have further strained the system.
Throughout 2022, sources described the state’s C&D network as a fragile one with little room for error.
“Massachusetts is notorious for having a lack of in-state disposal capacity for C&D materials, but the processing capacity shortage has slowed daily throughput and put a lot of pressure on the C&D market,” said Anthony Martignetti, CEO of a self-founded company that is building a new recycling and transfer facility in the area.
“As C&D processors rely on multimillion-dollar processing systems, recyclable end markets, disposal facilities, third-party rail carriers and all other aspects of their facilities to run at constant full capacity to meet demand, it should be expected the weakest link will occasionally fail.”
Adapting to recycling standards
Massachusetts’ disposal bans on C&D materials such as certain categories of wood, clean gypsum wallboard, asphalt, pavement, brick and concrete have been in place for more than a decade. The state’s 15% MPS for C&D handling facilities, enacted in January 2020, is an extension of that approach.
According to a December update, 16 of 18 C&D recyclers were compliant (with the remaining two optimizing equipment) along with all 11 C&D transfer stations. Industry participants say the MPS has slowed processing speeds because all loads with materials covered by the standard must be sorted. This means that a facility which once had transfer capacity for a certain tonnage of material is likely not handling that same amount of material anymore.
Some haulers also say the change has complicated their ability to move materials that aren’t as easily recyclable and may count against a facility’s MPS calculations.
One common example is commercial roofing material, largely made up of polystyrene foam and rubber. The material is lightweight, low value and prevalent in the Boston market as many buildings are being demolished. Jimmy Georgoulakos Jr., president and owner of Dynamic Waste Systems, said it’s not uncommon to fill up three trailers from one job and struggle to find a home for it.
"Nobody wants these loads and you get load rejections and it's from facilities across the whole state,” he said this past fall. "It's almost crippling for us to deliver a load like this to somebody.”
CDRA’s Thomas, who is also president of mining, materials and solid waste at The Mount Group in New Jersey, described this material as a “nuisance waste” that can be challenging to manage. Thomas said landfill operators don’t like the material due to concerns around per- and polyfluoroalkyl substances (PFAS) and because it blows around. Plus, it is becoming less common for regional mass burn combustion facilities to take C&D loads.
Georgoulakos will sometimes space out how much of this material he sends to facilities at one time and hope that relationships with local operators will facilitate the process.
Mike Mowbray, president of Recycling Solutions, is one such facility operator. Transportation costs are expensive, and hitting minimum weight limits for outbound trailers is important, so it’s not in his interest to ship a full load of roofing foam. As disposal capacity continues to decline in the region, transportation and disposal costs to export material have gone up.
"The transportation cost was a fraction of the disposal overall,” Mowbray said in the fall, citing earlier periods when in-state disposal was an option. "When we were going local it didn't matter as much.”
Another commonly discussed category is bulky waste, which accounted for an estimated 24% of material at state C&D facilities in 2020. This includes furniture and other material that might come from a house cleanout. Junk collection companies may pull valuable metal out first before delivering their loads, and what’s left is not simple to process.
"It's almost like you have to deconstruct the couch,” said Martignetti. "Yes, it has recyclable contents. But to actually be able to get to them, separate them, it's challenging."
MassDEP commissioned a recent study that assessed five of the state’s most active facilities handling bulky waste. It found 37.3% of bulky material was already covered by the state’s waste bans and 29.6% had “additional recoverability potential.”
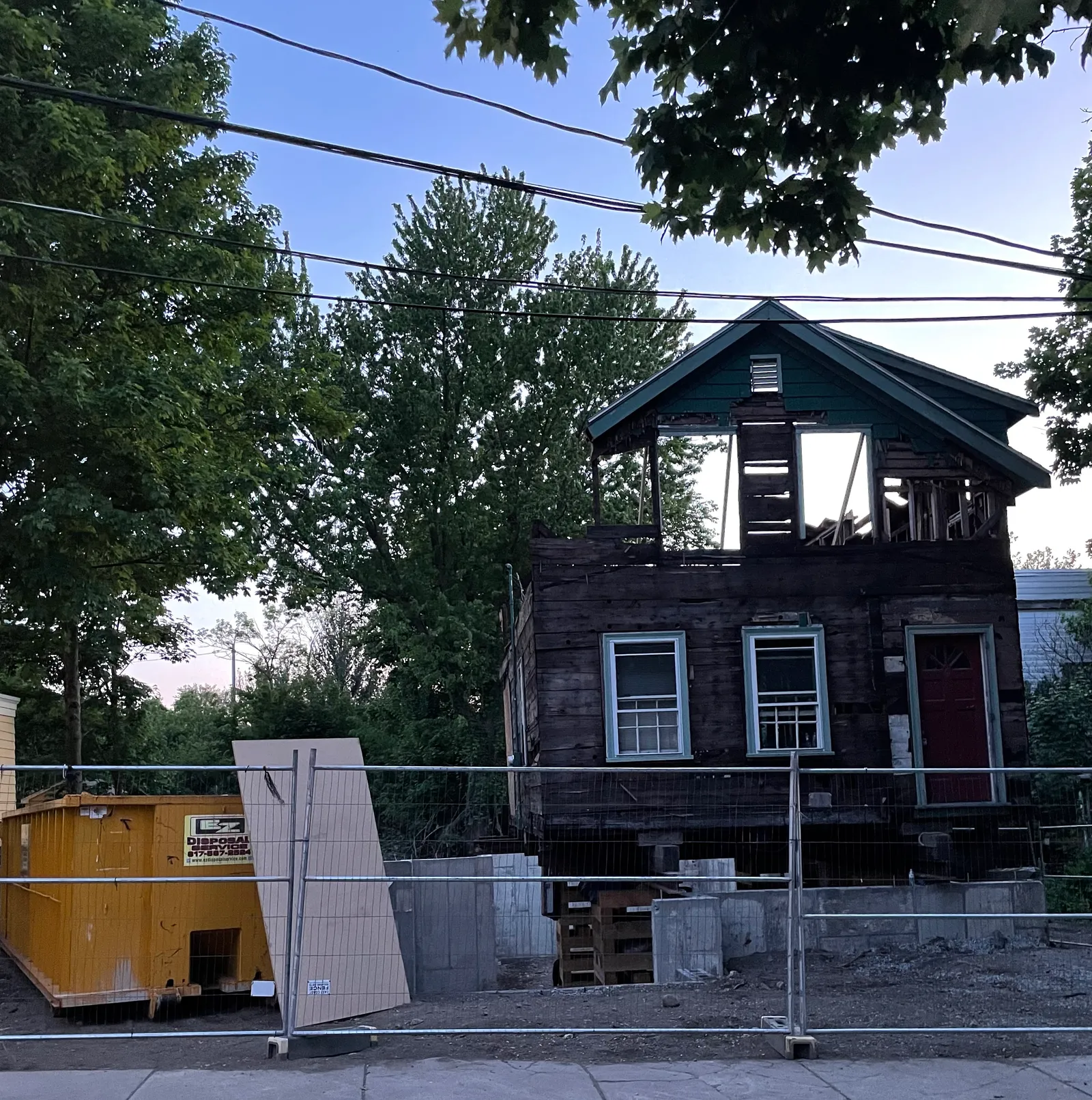
John Fischer, MassDEP’s branch chief of commercial waste reduction and waste planning, cited viable bulky materials such as metal file cabinets, cardboard boxes, lumber and yard debris. While Fischer didn’t have specific details on other streams cited as challenges, such as roofing foam or carpet, he said it was accurate that the MPS rules may have led to slower processing speeds. But Fischer described that more as a near-term challenge.
Fischer said in September that while some facilities may be taking more time to process material he expects the system will become more efficient with ongoing infrastructure investments.
“Once they do that, every ton they pull out like that is a ton that does not then have to go probably by rail to a landfill out of state,” he said.
When one of the state’s largest C&D recyclers was asked whether the MPS shift may have affected the system’s efficiency, and how it made decisions about which materials to accept, the company said broadly that it had adjusted to the new normal.
“We continue to work towards overachieving on these important goals set by the DEP and proactively investing in our facilities in hopes of offsetting the fragility of end disposal infrastructure and the recycled goods market,” Mary Urban, WIN Waste’s director of communications, community engagement and marketing, via email in mid-November.
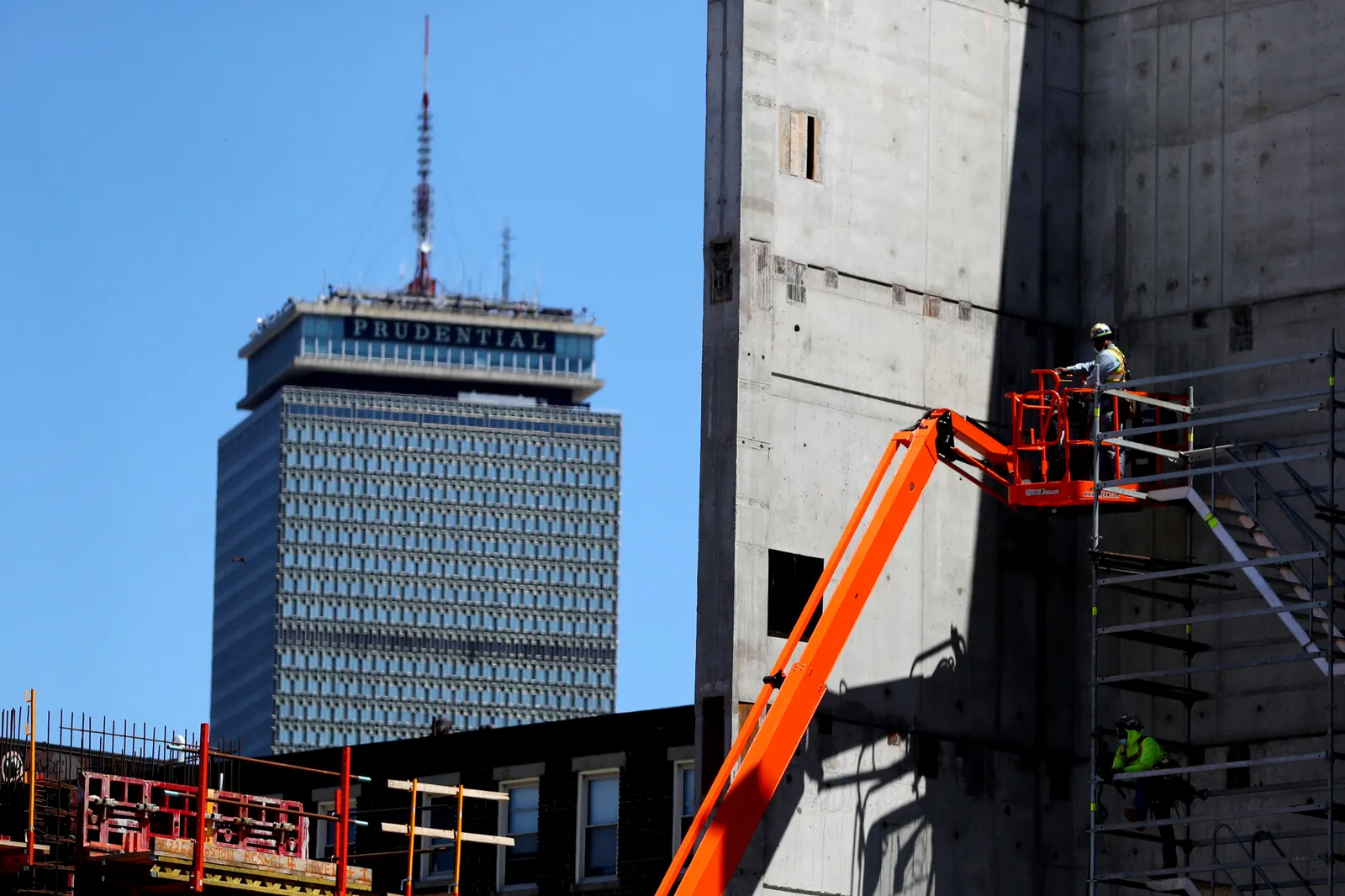
Operating constraints
Local operators say broader transportation trends are similarly challenging.
Georgoulakos said it used to be possible for a driver to do eight to 10 roll-off loads around Boston per day, or five loads in more suburban areas due to the distance. “That productivity has changed,” he said, citing multiple local facility closures, to the point that Dynamic has often turned down work lately.
"It didn't really matter because the tonnage dropped in 2020,” he said, but as of summer 2021 “it became really difficult to move the stuff in Greater Boston because there was almost no place to go with it” and haulers started driving to more distant facilities.
Regardless of the location, haulers now encounter hourslong wait times to tip, abrupt closures when facilities hit capacity or have transportation issues and multi-day stretches during which some locations won’t take material at all. Operators say they are similarly constrained.
"The only reason why we stop accepting material is because we can't ship material,” said Mowbray, adding that this limits him from running at full capacity. "I can never do 1,000 tons per day because I don't have 1,000 tons a day of outbound capacity.”
Last year’s recurring rail strike threat was also a factor, with operators seeing temporary disruptions on top of an already complicated system.
“Even without a strike, the instability between rail carriers and labor has impacted our industry and many others,” said Urban, noting in November that WIN Waste — the industry’s largest waste-by-rail operator — was in daily communication with its rail partners.
The National Waste & Recycling Association has also been engaged on this issue. Lew Dubuque, Northeast vice president, said in October that labor constraints over the summer led to delays in receiving or moving rail cars. While Dubuque described rail companies as receptive to industry concerns, he said the capacity-constrained Northeast still has limited options.
"Truck capacity is hard because Massachusetts has the truck weight limits, so that limits the amount that our members can get out by truck,” said Dubuque. "If there was no [rail] service, for even a short period of time, it would have been a disaster."
While President Joe Biden signed legislation to avert a strike — a move applauded by NWRA — other challenges remain. Multiple participants in the market who aren’t vertically integrated said that as areas such as Maine cut off C&D imports the next most likely destination is upstate New York. But finding a way to move material economically, especially with labor availability issues and fuel costs, isn’t simple either.
"There's disposal capacity and then there's affordable disposal capacity,” said Mowbray. "The market's been getting crazy so the numbers keep jumping up.”
For Georgoulakos that means directing more of his company’s trailer hauling operations to partners’ facilities, rather than hauling material from his own job sites.
"I'm denying orders to customers with trailers,” he said, “so my tractor trailer fleet can maintain the hauling out of these transfer stations.”
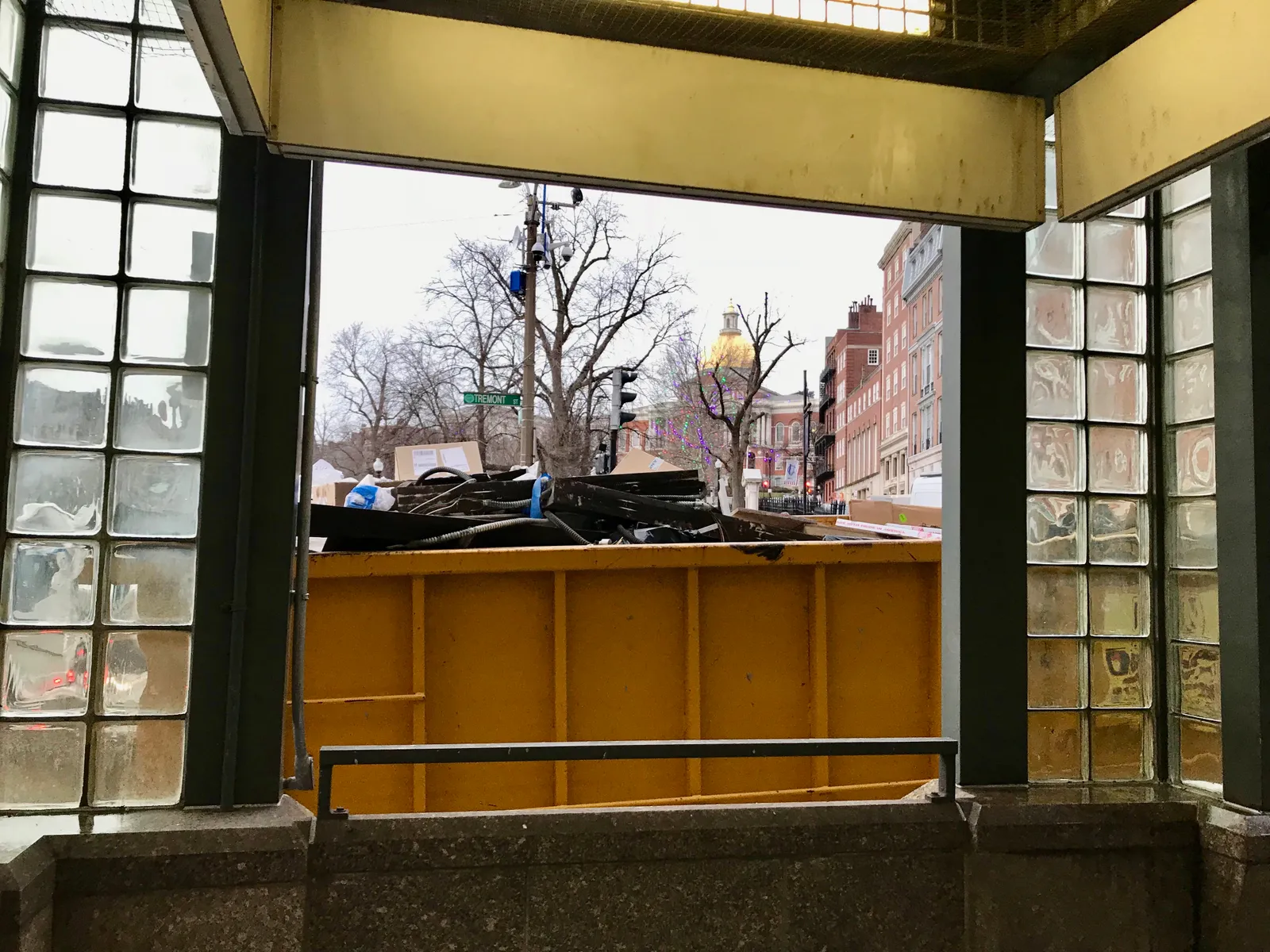
Looking ahead
With ongoing construction slated for the region, C&D costs are expected to keep rising.
Thomas described C&D tip rates in Massachusetts as higher than in the New York and New Jersey market. As labor and transportation expenses escalate, and the regional market gets consolidated by larger players, he anticipates that trend will continue. While Thomas said MassDEP has been active with grants for upgrading processing equipment, he and others hope to see more activity on developing end markets and capacity for other disposal options.
Fischer said the best way to ease logistical constraints “is not so much by developing new disposal capacity” but to try and “reduce the amount of C&D material and all waste” within the state.
MassDEP recently launched a deconstruction working group and also offers resources for job site separation. Fischer pointed to gypsum wallboard as one material that benefits from separate collection, while recognizing this may not be feasible at all job sites and ongoing work will be required to expand C&D options.
In the meantime, state data shows non-MSW exports (a category that primarily refers to C&D) increased from 2019 to 2020 and that trend is likely to continue.
The market is seeing C&D processing and transfer capacity additions by companies such as North Andover Waste Systems and an upcoming rail-served facility from Martignetti that is now set to open in 2024. Even with those additions, local operators say market conditions are leading haulers to get more creative with how they manage loads, pre-book tonnage at facilities when possible and become more selective about the jobs they take.
Martignetti anticipates it will eventually become more common for C&D facilities to primarily collect and process material within smaller regions, especially as electric collection vehicles become more prevalent. But in the meantime, local haulers must go farther.
"If you're not willing to drive you're really hurting if you're relying on the Greater Boston areas' facilities,” he said. “This just needs to get to a level where everybody can reasonably operate and get through their day in the state.”