In the five years since China disrupted the global flow of recyclable materials with its National Sword policy, the U.S. has seen investments in new or upgraded end market infrastructure worth hundreds of millions of tons in capacity.
Yet debate continues over the extent to which that country’s scrap import policies influenced the domestic investment wave. While some believe other environmental and geopolitical factors bear greater responsibility for the push to improve curbside material cleanliness and boost domestic markets, commodity experts agree a shift has clearly occurred.
“National Sword made it very clear that we can no longer rely on volatile foreign markets for solid waste management of packaging,” said Steve Alexander, president and CEO of the Association of Plastic Recyclers. “It reinforced the fact that we're going to have to create the infrastructure here in this country.”
The policy, which officially took effect in 2018, banned the import of 24 scrap materials into China (including mixed paper and mixed plastics) and limited the contamination level for remaining imports to 0.5%. Other markets, such as India, Indonesia and Malaysia, emerged as strong players to accept the affected materials, but no single country could fill the gap.
Investments in domestic end markets were occurring prior to National Sword, but “if you look at the trend line, it certainly appears that it accelerated post-National Sword,” said Resa Dimino, managing principal at RRS and managing partner at Signalfire Group. “We've seen pretty significant investments both on the paper and the plastic side to develop domestic markets.”
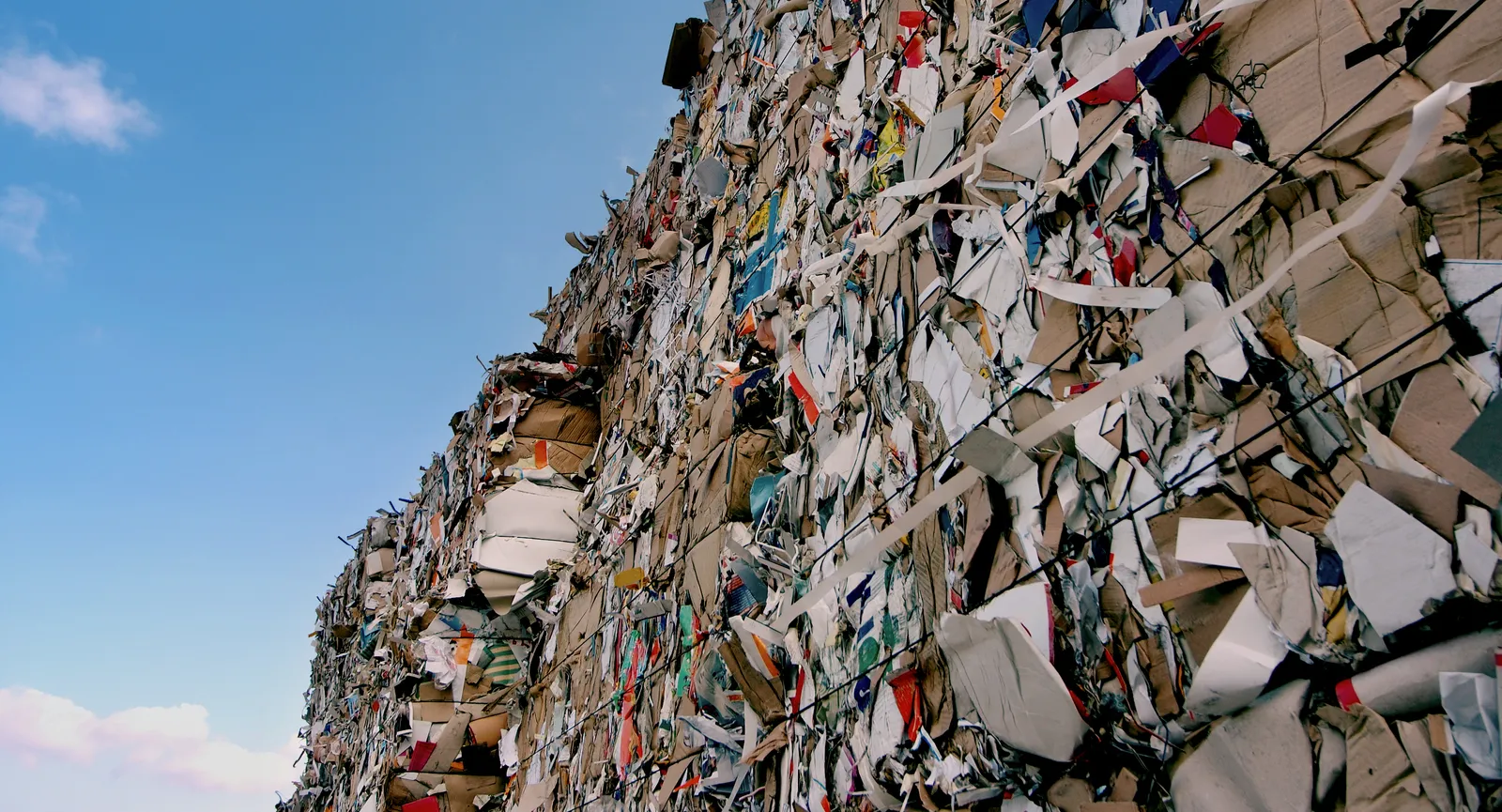
Paper picks up
The Northeast Recycling Council began tracking domestic recycling paper capacity increases in 2018. It noted that some expansions already had been planned prior to National Sword because of growing box demand as e-commerce sales surged — a trend that further accelerated during the pandemic — but also said China’s material bans spurred additional domestic capacity increases.
NERC’s recently updated list cites 28 new recycled paper mill projects since 2018, 17 of which have been completed, for a total of 8 million tons per year of increased capacity for OCC and mixed paper. Overall, mills moved away from handling feedstock grades in receding demand, such as newsprint, and added capacity for processing OCC. The nine projects still in the works — including a Pratt Industries mill in Kentucky and a Cascades mill in Virginia — are scheduled for completion this year or next year.
“It’s common knowledge what’s been going on with paper mills the last three to four years,” said Myles Cohen, founder of consulting firm Circular Ventures and former president of Pratt Recycling. “There’s a resurgence of interest, particularly in the containerboard business… We've not seen anything like this in a very, very long time.”
Brands and retailers are leading the charge toward more recycled content in products with new or expanded sustainability commitments. Their actions often are driven by consumers’ desire for more recycled content in packaging as well as mandates in certain states.
“The common thread with most of the new capacity projects is 100% recycled content — or a very high percentage of recycled content — because that is where the market is going,” Cohen said.
NERC’s analysis points out that much of the new capacity is coming online at existing or previously closed mills that have either reopened or been upgraded.
“It’s an advantage if you’re working with an already existing facility,” said Chaz Miller of Miller Recycling Services, who compiles the list for a regional task force that includes NERC. “You don't need to worry about zoning. You've already got your transportation routes worked out. You've already got base permits.”
An upgraded mill needs new permits if it’s producing a different product, he said. For example, multiple mills are transitioning to producing recycled brown pulp — a product experiencing a notable demand boost. Recycled pulp is considered a cleaner material than fiber recovered curbside, because it has been processed, and does not face the same import bans. In recent years it has become a roundabout way to keep fiber flowing into China and other Southeast Asian countries.
Foreign and domestic companies alike have boosted their recycled pulp production at U.S. facilities. Nine Dragons has been building up its U.S. network of pulp mills, including facilities in Maine and West Virginia, with the intent of shipping much (if not all) of the produced pulp back to its paper mills in China. Last year, Celadon committed to investing $155 million in a U.S. headquarters and recycled brown pulp production facility in Georgia. And last month, CellMark announced a partnership with Total Fiber Recovery to build an $80 million recycled pulp production facility in Chesapeake, Virginia.
Recycled pulp traditionally “has not been a big market in the U.S.” and instead existed as a niche product, Cohen said. But now, “hundreds of thousands of tons of capacity are coming online to clean up recycled paper and make it eligible and legal to import into countries that were putting restrictions on ‘waste paper.’”
Progress for plastics
Investments in end markets for plastics similarly have accelerated. But compared with paper mill investments, “it's harder to get the data on the plastic industry because many of those facilities are done by companies that either make resin, or in some cases even make bottles or other products,” Miller said.
Continuus Materials, which converts recycled paper and plastic into building materials, has received multiple investments for expansion, including from a subsidiary of hauler and MRF operator WM. And the U.S. subsidiary of Thailand-based plastic manufacturer PTT Global Chemical recently announced that it will build a facility in Ohio to manufacture recycled PET and polyethylene into various products; Rumpke Waste & Recycling will supply the facility with plastic bales.
Dimino explained that many investments target a specific material, often one that experienced export challenges. Little PET and HDPE had been exported prior to National Sword, whereas mixed plastics regularly were exported.
“We’ve seen a lot of PET investments and PET reclaimers expanding, both in terms of capabilities and in terms of throughput,” Dimino said. “The same is true with HDPE and the new markets and sorting facilities developing around polypropylene, which was one of the primary materials that was exported.”
APR’s Alexander cites optical sorters as a leading technology that prompted change over the last decade, including allowing black plastic sortation. Optical sorter adoption rose over the past five years to the extent of becoming mainstream.
“And there has been a tremendous amount of investment in wash lines and processing capacity over the last three years — to the point where we have excess capacity — and there's even more slated for investment now,” Alexander said.
Industry and brand collaborations are another private investment strategy. Last year, for example, Dow, LyondellBasell and NOVA Chemicals announced $25 million worth of investments in a Closed Loop Partners fund to boost recycling technology, infrastructure and markets for polypropylene and polyethylene.
Companies are also investing in secondary plastic recycling facilities, or PRFs. As with paper projects, some PRF investments had been in the works before National Sword, but “what we discovered in the first round is a majority of those didn’t work out,” Miller said. For instance, the QRS Maryland plastics recycling facility opened in 2015, suspended operations in 2017 and closed for good in 2018, which sources say largely occurred because of unfavorable market conditions at the time. A separate New Jersey PRF project announced in 2017 became ensnared in regulatory and legal battles and hasn’t come to fruition.
A new wave of secondary plastics recycling investments has emerged, and sources say the timing and resin pricing seem more viable than during the initial PRF movement. In 2018, Chinese-owned Roy Tech Environ said it would open a plastics recycling facility in Alabama to ensure its factories in China would have enough recycled plastic amid that country’s import restrictions. Republic Services recently announced it will build a PRF in Las Vegas that will produce 100 million pounds per year of recycled plastic; it will be the first of multiple similar facilities and should begin operations next year.
The infrastructure division at investment firm Closed Loop Partners recently invested $5 million in Myplas to develop a flexible film recycling plant in Minnesota. The group is interested in making more investments in post-MRF infrastructure, with a focus on addressing market gaps for harder-to-recycle plastics like LDPE and HDPE.
"Looking at how to manage some of these more challenging formats, like flexibles, is going to continue to be a core focus for our team from an investment perspective," said Jennifer Louie, an executive director at Closed Loop Partners.
Chemical recycling, or non-mechanical recycling, is another area gaining steam — albeit with plenty of controversy. Chemical recyclers say they provide solutions for handling hard-to-recycle plastics that don’t otherwise have markets, while critics say the concept is a distraction from reducing the use of certain plastics and too many projects focus on creating fuel products.
Agilyx debuted a polystyrene conversion plant in Oregon in 2018 that remains active. In 2020, INEOS Styrolution and AmSty announced plans for a polystyrene recycling plant in Illinois that would use Agilyx’s pyrolysis technology. Last month, Dow and Nexus Circular announced plans for a pyrolysis plant in Texas that will handle hard-to-recycle plastics collected curbside.
Alexander says plastics recyclers consistently make investments in new technologies and other infrastructure, but they have a problem securing a suitable supply of recyclable materials.
“The problem isn't recycling capacity; the problem is getting the supply of material to the recyclers,” he said. “Recyclers are only able to recycle the material that's available to them in the form that's available to them. Our design guidance is out there telling the world how to design packaging in order for it to be successfully recycled.”
Even commonly recycled resins like PET are in short supply compared to the amount needed to meet recycled content targets from brands, state governments and plastic advocacy groups, many of which are slated for 2025.
“You need to collect something like three times the amount of PET you're collecting today in order for us to get to 35% or 50% content,” Alexander said. “And it's not a simple supply-demand equation, because we depend on the communities’ recycling programs running well.”
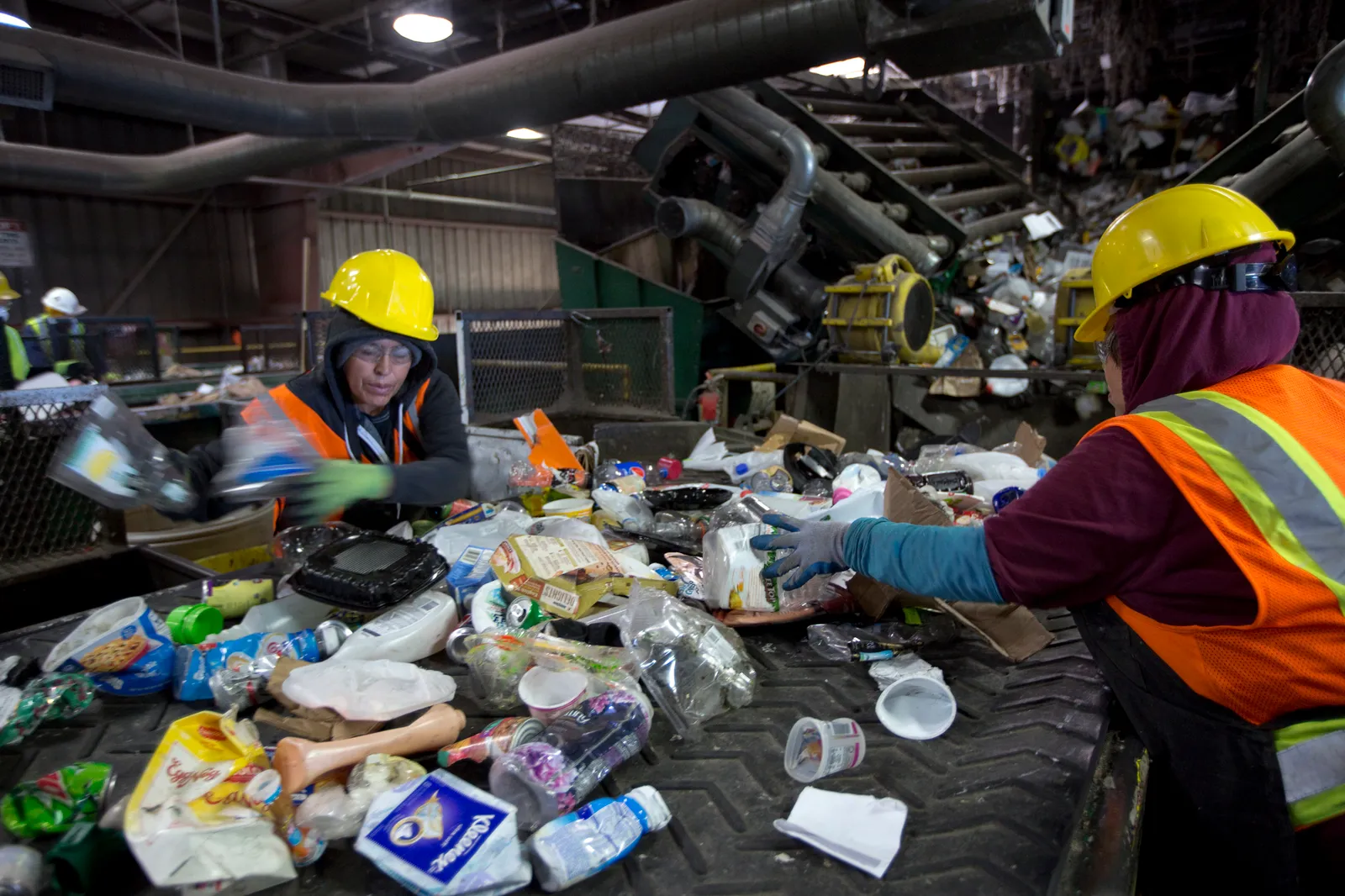
Finding and filling gaps
While a lot has happened in the last five years, Alexander says it’s still not enough time to fully transform domestic market infrastructure in the U.S.
“Now that folks are focused on it, they expect this whole system to snap its fingers and change overnight,” he said. “It certainly doesn’t happen that way… It’s extremely complex.”
As evidenced by early PRF projects fizzling, factors including supply, demand and commodity pricing can play into the equation. Plus, companies themselves may slow the process when taking the necessary time to weigh major capital expenditures. Such purchases mostly are funded solely by private investments; government assistance could be an accelerating factor, but it is not prevalent.
“There’s definitely some support from the government to make it happen, but I don’t think it’s driven by the government,” Signalfire’s Dimino said. “Private companies are taking advantage of a moment in the marketplace where there’s extremely high demand for recycled materials.”
Despite last year’s move by the U.S. EPA to establish a recycling-focused grant program funded by the Infrastructure Investment and Jobs Act, instances of government assistance typically are occurring at the state and local level. Michigan, Colorado, and Washington are among the leading states putting resources toward developing recycling-based businesses, Dimino said. She added that over the last few years more states have passed mandatory minimum recycled content rules, and policymakers want the materials collected in their state to go into new packaging.
“That’s an important factor that certainly supports the development of markets and infrastructure domestically,” Dimino said. “Since 2020, we’ve seen a fair amount of activity, and I would expect that to continue as policymakers want to see more circularity.”
Sources point to the West Coast — previously a significant exporter of material to Asia — as having a capacity gap, and that presents opportunities for more investments.
“The West Coast still could use more capacity, certainly, on the mixed plastic and polypropylene recovery front,” Dimino said. “And I think that’s true of paper as well. A lot of the mill announcements and upgrades you see are in the Midwest and Northeast.”
National Sword may have accentuated the value of mitigating contaminants and producing clean material, but the jury is out on whether domestic investments in the last five years noticeably moved the needle toward cleaner domestic curbside recyclable commodities.
A leading reason is the amount of non-recyclable material residents put in curbside bins — including masks since the pandemic began — which sources say underscores the need for education and cleanup work along the entire value chain. Material reclaimed from commercial entities like big box stores consistently is cleaner than that from residential recycling programs.
“The people that I talk to say the contamination has not changed a whole lot from what it was several years ago. Many say it’s gotten worse,” Cohen said.
Investments ebb and flow
Like commodity prices, investment waves are cyclical. Although sources hesitate to offer firm predictions of how long this cycle will last, they generally anticipate that current economic conditions could prompt a near- to medium-term recycling investment slowdown.
Plus, some recyclers are exhibiting caution with capital expenditures to gauge supply and demand as new capacity comes online.
“You can’t just build a paper mill or new plastics facility… and expect that all of the additional volume that you manufacture is just going to get sold,” Cohen said. “The packaging industry — no matter what the substrate is — is very dependent on consumer spending trends.”
Even if investments do decelerate soon, that doesn’t necessarily signify an end to the post-National Sword recycling resurgence.
“Recyclers are always updating their technology as well as creating solutions. It’s a very dynamic industry,” Alexander said. “I think people have woken up to a lot of things because of National Sword, but a lot of other factors also influence where the industry goes next.”